- Home /
- Navigating Supply Chain Risks for Silicone Hoses with Goodflex Rubber
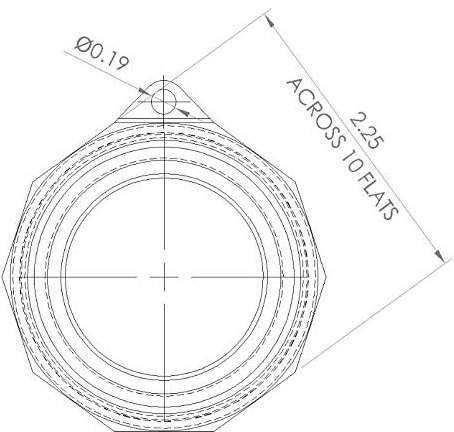
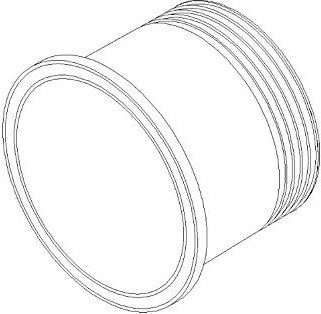
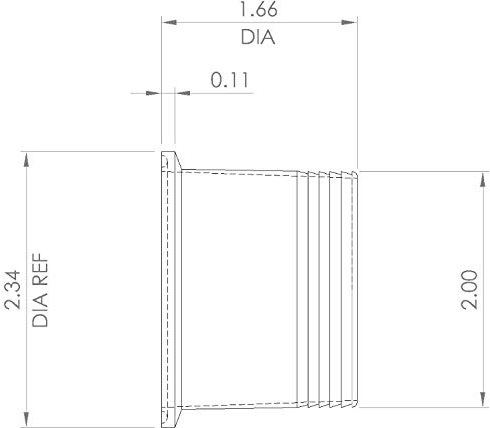

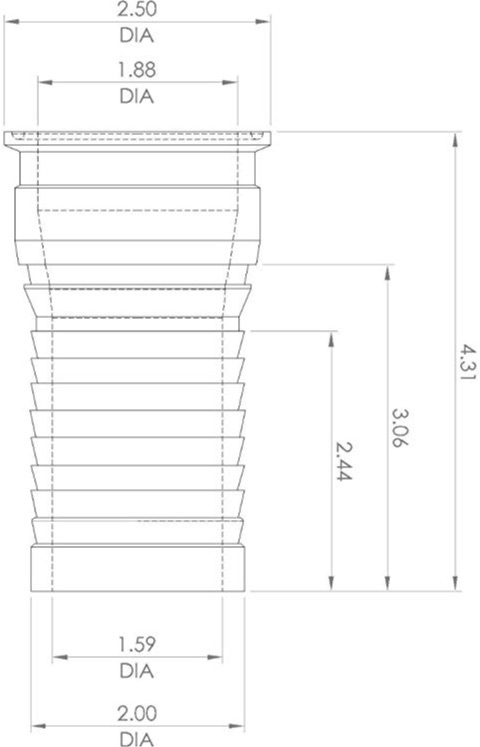
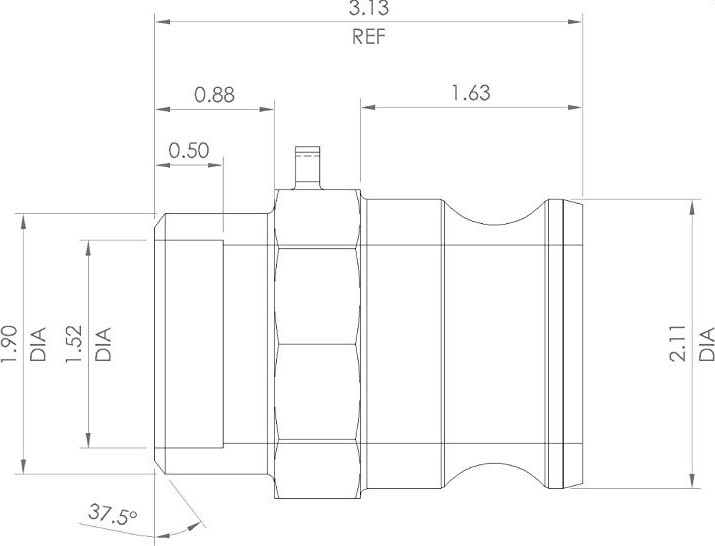
Blog
Navigating Supply Chain Risks for Silicone Hoses with Goodflex Rubber
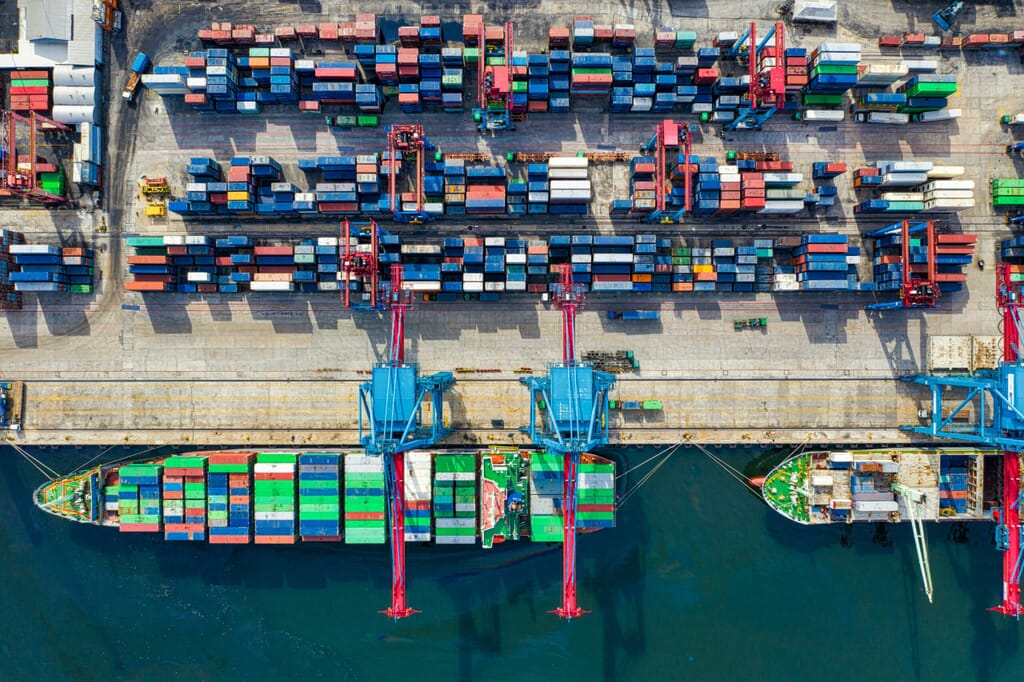
Navigating Supply Chain Risks for Silicone Hoses with Goodflex Rubber
At Goodflex Rubber we recognise the importance of efficient and reliable fluid transfer products and how essential they are in our everyday lives. From high temperature applications to pharmaceutical transfers, our world relies on these often-overlooked connections.
Understanding the risks at each stage of the supply chain gives us an advantage in overcoming arising concerns. This proactive approach ensures that potential problems are identified and resolved before they can impact your operations.
Identifying Risks in the Supply Chain for Silicone Hoses
Supplier Reliability
Evaluating the dependability of our raw material suppliers is crucial. Any disruptions or inconsistencies in supply can lead to delays in production, affecting our ability to deliver on time.
Quality Control
Ensuring that all materials and finished products meet quality standards is essential to minimise the risk of defects and recalls.
Logistics Management
Effective management of logistics, including transportation and warehousing, reduces the risk of delays and damage during transit, ensuring that your products arrive safely and on time.
Mitigating Supply Chain Risks for Silicone Hoses
Inventory Management
Maintaining optimal inventory levels ensures that we can meet customer demands even during unforeseen supply chain interruptions.
Supplier Partnerships
Building strong relationships with our suppliers enables better communication, more reliable delivery schedules, and quicker resolution of issues.
Advanced Planning
Utilising advanced planning systems allows us to anticipate potential supply chain disruptions and develop contingency plans accordingly.
A Collaborative Approach
At Goodflex Rubber, we believe that collaboration is key to effectively mitigating supply chain risks. By working closely with you, our team provides a purchasing experience tailored to meet your specific transfer needs. Serving industries such as automotive, off-highway, rail, pharmaceutical, food-grade and renewable energy, we offer solutions designed to keep you moving forward.
The Rising Risks in Supply Chain Management for Silicone Hoses: Is Offshoring Worth the Uncertainty?
In the last decade, offshoring has been a common strategy for companies looking to reduce costs, increase efficiency, and tap into global talent pools. But in recent years, the landscape has changed dramatically. Supply chain risks have become a critical concern, driven by geopolitical tensions, global pandemics, and unpredictable market fluctuations. Companies in industries like construction, automotive, agriculture, and especially the off-highway sector are now questioning whether the benefits of offshoring still outweigh the growing uncertainties.
At Goodflex Rubber, where we design, manufacture and supply advanced silicone and organic rubber hoses, mouldings and assemblies, we’ve seen first hand how the volatility of global supply chains impacts businesses. As supply chain risk grows, companies are rethinking their strategies—seeking stability through reshoring or nearshoring to better manage these emerging challenges. Here’s why uncertainty in offshoring is at an all-time high and how you can mitigate these risks.
Geopolitical Tensions and Trade Barriers for Silicone Hoses
The rise of trade barriers, tariffs, and geopolitical disputes have made sourcing from certain regions far more complicated. Countries that were once reliable manufacturing hubs may now face export restrictions or escalating costs due to trade wars. As a result, the cost advantage of offshoring is diminishing.
Take the case of raw materials used in rubber manufacturing. If the country where your supplier operates faces new tariffs, those increased costs are passed along to you. This unpredictability makes it harder to budget, and businesses risk interruptions if access to essential materials becomes restricted.
Supply Chain Disruptions from Pandemics and Natural Disasters
The COVID-19 pandemic highlighted the fragility of global supply chains. Manufacturing delays, shipping constraints, and fluctuating demand disrupted industries across the board. For companies relying on offshore suppliers, especially in regions hit hard by lockdowns, lead times were dramatically extended, causing production delays and increased costs.
In the off-highway industry, where equipment downtime can cost thousands per day, such disruptions can have a long-term financial impact. Global shipping, while seemingly reliable, is also susceptible to natural disasters that can shut down ports, damage infrastructure, and further disrupt schedules.
Rising Transportation Costs for Silicone Hoses
Offshoring typically means relying on international shipping to move goods from distant countries to your doorstep. But transportation costs have risen substantially due to fuel price increases, global port congestion, and shortages of shipping containers. A supply chain that once seemed cost-efficient may now come with far more significant transportation fees, eroding the initial savings from sourcing materials or parts offshore.
At Goodflex Rubber, we’ve seen how important logistics can be to maintaining smooth operations. When delivery delays occur due to increased transportation times or logistical bottlenecks, it can leave manufacturers scrambling for alternatives. What used to be a cost-saving strategy could now be costing you in the form of delays and lost revenue.
Quality Control and Compliance Issues for Silicone Hoses
One of the biggest risks of offshoring is the potential compromise in quality control. Managing production standards from a distance can be tricky, and inconsistent product quality or failed regulatory compliance can quickly become costly problems. If an offshore supplier provides substandard materials or components that don’t meet stringent industry standards, it can lead to costly recalls or damage to your reputation.
Goodflex Rubber has long been committed to maintaining rigorous standards, ensuring our components meet the highest specifications. However, for companies offshoring their production, they may find it difficult to consistently manage and monitor quality without direct oversight. And in industries like construction or mining, where safety and reliability are non-negotiable, this could pose a major risk.
Sustainability and ESG Considerations
More companies are now incorporating Environmental, Social, and Governance (ESG) goals into their supply chains. Offshoring to countries with less stringent environmental regulations or questionable labour practices can negatively impact a company’s sustainability credentials. As customers and investors demand more transparency and accountability, businesses are increasingly pressured to ensure their offshore suppliers meet ethical standards. Failing to do so can lead to reputational damage, regulatory penalties, or loss of market trust.
Reshoring and Nearshoring Silicone Hoses: Alternatives to Offshoring
As the risks of offshoring grow, many companies are exploring reshoring (bringing production back to their home country) or nearshoring (sourcing from countries geographically closer). Both options offer more control, reduce transportation costs, and help companies stay more agile in times of crisis. Additionally, local or regional supply chains are often more resilient, as they can adapt quickly to changes in demand or disruptions.
For companies in the off-highway industry, reshoring and nearshoring strategies could reduce downtime and improve overall reliability. By working with local suppliers, businesses can ensure faster delivery times, better quality control, and a more responsive supply chain.
At Goodflex Rubber, we understand that in an increasingly uncertain world, having reliable and responsive suppliers is critical.
Conclusion: Is Offshoring Worth the Risk Anymore?
The era of cost-driven offshoring is evolving. While offshore sourcing still has its place, the growing risks make it less attractive for many companies, especially those in industries like off-highway manufacturing that rely on precision, reliability, and timely deliveries. Geopolitical instability, rising transportation costs, supply chain disruptions, and the need for greater sustainability are driving more companies to consider reshoring or nearshoring.
In today’s market, building a resilient supply chain is more important than ever. Choosing the right suppliers could be the key to navigating these uncertain times.
To learn more about how Goodflex Rubber can help you build a more resilient supply chain, visit us at www.goodflexrubber.com or email technical@goodflexrubber.com